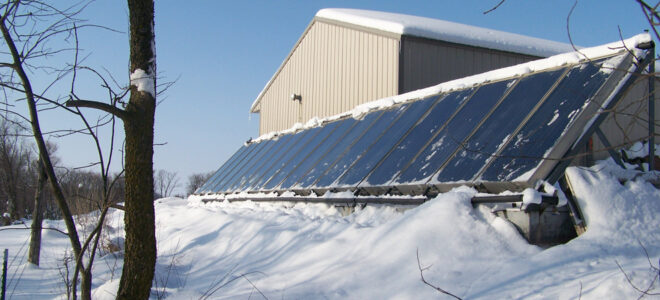
As the world moves towards a future of sustainable transportation, hydrogen-powered vehicles are gaining traction as an attractive alternative. Utilizing aluminum tubes to store and transport hydrogen can be a significant advantage in developing such vehicles.
Aluminum is light, durable, and resistant to corrosion, making it the ideal material for improving vehicle efficiency and safety while reducing costs. This article will explore how harnessing the advantage of aluminum tubes in hydrogen fuel vehicles can help reduce emissions while providing accessibility to clean energy solutions.
Advantages of Using Aluminum Tubes for Hydrogen Fuel Storage
The use of aluminum tubes for the storage of hydrogen fuel offers several advantages when compared to other materials. For starters, aluminum is lightweight, which makes it easy and inexpensive to transport. Additionally, it has excellent corrosion resistance properties and can withstand high pressure and temperatures.
This means that hydrogen fuel stored in an aluminum tube is less likely to be damaged or degraded by environmental conditions. Aluminum also has a much higher strength-to-weight ratio than steel or plastic, making it perfect for holding large amounts of pressurized hydrogen without being too heavy. Furthermore, due to its low cost and ease of fabrication, an aluminum tube provides a great way for manufacturers to create efficient and reliable storage containers at a reasonable price point.
Finally, because aluminum is nonmagnetic and nonconductive it can safely contain the electricity generated through electrolysis to produce hydrogen gas from water molecules — something that cannot be done with other materials such as steel or iron tubing. All these factors make using aluminum tubes ideal for storing hydrogen fuel in vehicles powered by this energy source.
Manufacturing Processes and Design Considerations for Aluminum Tubes

Source: hydro.com
Aluminum tubes are becoming increasingly popular for use in hydrogen fuel vehicles. This is due to their lightweight and durability compared to other materials, making them well-suited for the demanding conditions of a fuel vehicle. To effectively utilize aluminum tubes in hydrogen in fuel vehicles, it is important to consider several manufacturing processes and design considerations. The first step when using aluminum tubes in hydrogen fuel vehicles is selecting an appropriate alloy grade that can withstand the harsh environment present inside a fuel cell.
Aluminum alloys containing copper or manganese tend to be best suited for this purpose as they provide superior strength and corrosion resistance properties. Additionally, specific heat treatments must be applied during the manufacturing process so that any residual stresses which could cause issues with weldability are removed from the tube itself. In terms of design considerations, various parameters should also be taken into account while designing aluminum tubes used in these applications such as wall thickness and maximum operating pressure levels among others.
These values must be kept within allowable limits based on safety regulations otherwise catastrophic failure could occur if exceeded beyond certain thresholds. Furthermore, consideration should also be given to surface finish requirements along with the overall geometry of each part depending on its intended application within a particular system setup.
Overall, by taking into account key manufacturing processes and design considerations when using aluminum tubes in hydrogen fuel cells, engineers can ensure the successful implementation of this material without compromising on quality standards or performance criteria set forth by regulatory bodies worldwide
Factors Affecting the Performance of Aluminum Tube Structures in Hydrogen Fuel Vehicles
The performance of aluminum tube structures in hydrogen fuel vehicles is largely affected by several factors. One factor is the weight-to-strength ratio, as lighter materials are more likely to increase the efficiency and speed of the vehicle. Additionally, the durability of aluminum tubes needs to be taken into account when used in such applications.
The corrosion resistance and structural integrity must remain high even after exposure to extreme temperatures or weather conditions for long periods. Furthermore, other considerations include whether or not there will be any catalytic effects on hydrogen production due to their material composition, as this could have an impact on engine performance.
Finally, it’s also important to consider how well they interact with other metals and components present within the system to ensure compatibility between all parts involved. All these aspects should be taken into consideration before making an informed decision about using aluminum tubes for building hydrogen fuel vehicles if optimal results are desired.
Conclusion
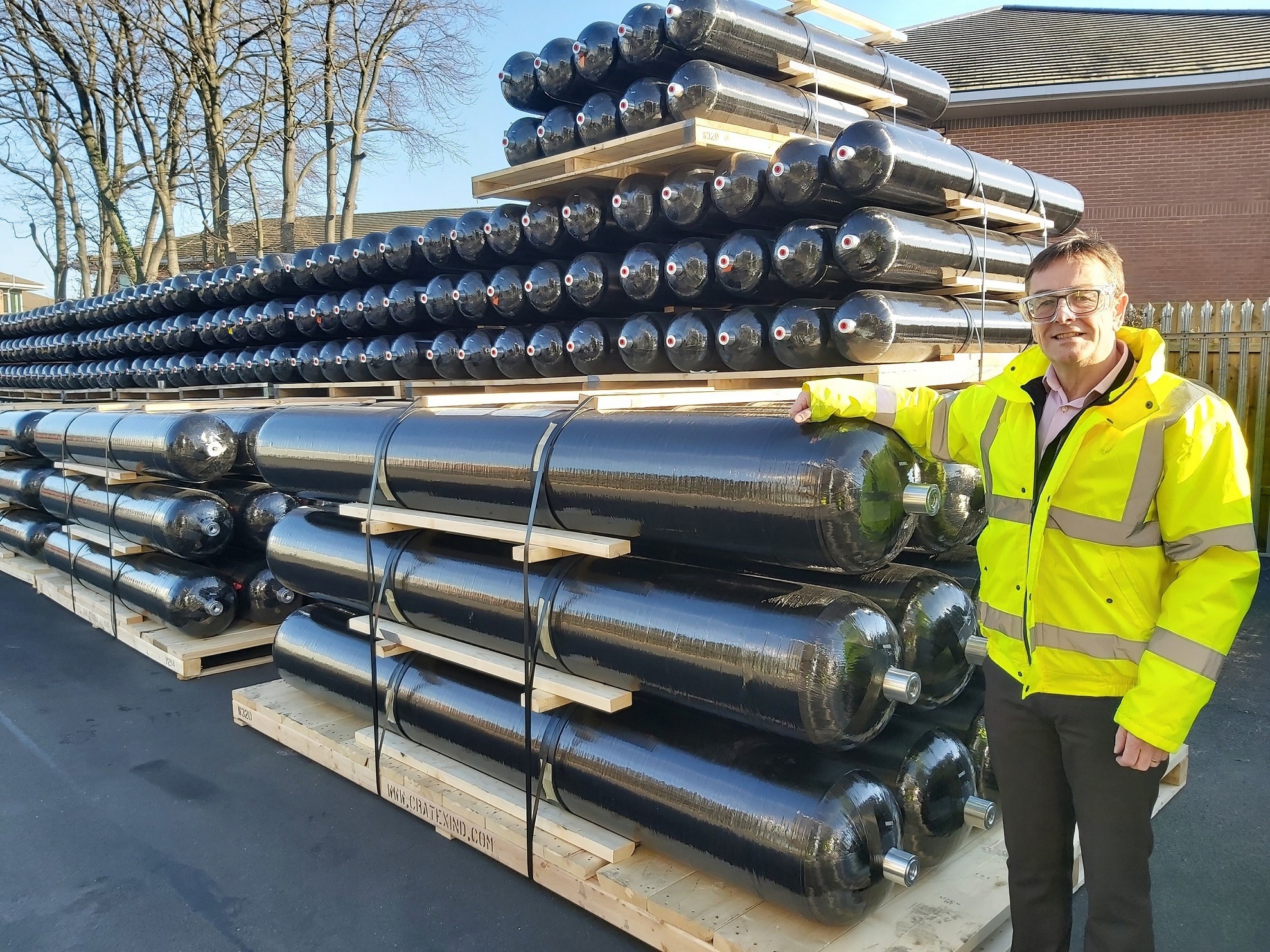
Source: azocleantech.com
Aluminum tubes are a great advantage for hydrogen fuel vehicles. They are lightweight, durable, and able to withstand extreme temperatures and pressures which make them ideal for transporting hydrogen safely and efficiently within the vehicle.
Aluminum tubes also help reduce costs associated with hydrogen storage compared to other materials such as steel or carbon fiber cylinders. Overall, using aluminum tubes in hydrogen fuel vehicles is an effective way of keeping costs down while still having a reliable energy source when needed.